Por favor, avalie esta postagem
Vários objetos de vidro criados em impressora 3D. Crédito: Grupo de Materiais Complexos / ETH Zurique
Os pesquisadores da ETH usaram um processo de impressão 3D para produzir objetos de vidro complexos e altamente porosos. A base para isso é uma resina especial que pode ser curada com luz UV.
Produzir objetos de vidro usando impressão 3D não é fácil. Apenas alguns grupos de investigadores em todo o mundo tentaram produzir vidro utilizando métodos aditivos. Alguns fabricaram objetos imprimindo vidro fundido, mas a desvantagem é que isso requer temperaturas extremamente altas e equipamentos resistentes ao calor. Outros usaram partículas cerâmicas em pó que podem ser impressas em temperatura ambiente e depois sinterizadas para criar vidro; entretanto, os objetos produzidos desta forma não são muito complexos.
Pesquisadores da ETH Zurique usaram agora uma nova técnica para produzir objetos de vidro complexos com impressão 3D. O método é baseado na estereolitografia, uma das primeiras técnicas de impressão 3D desenvolvidas na década de 1980. David Moore, Lorenzo Barbera e Kunal Masania, do grupo de Materiais Complexos liderado pelo professor da ETH André Studart, desenvolveram uma resina especial que contém plástico e moléculas orgânicas às quais os precursores de vidro estão ligados. Os pesquisadores relataram seus resultados na última edição da revista. Materiais naturais.
Luz usada para “crescer” objetos
A resina pode ser processada usando a tecnologia Digital Light Processing disponível comercialmente. Isto envolve irradiar a resina com padrões de luz UV. Onde quer que a luz atinja a resina, ela endurece porque os componentes sensíveis à luz da resina polimérica se reticulam nos pontos expostos. Os monômeros plásticos se combinam para formar uma estrutura semelhante a um labirinto, criando o polímero. As moléculas contendo cerâmica preenchem os interstícios deste labirinto.
Um objeto pode assim ser construído camada por camada. Os pesquisadores podem alterar vários parâmetros em cada camada, incluindo o tamanho dos poros: uma intensidade de luz fraca resulta em poros grandes; a iluminação intensa produz pequenos poros. “Descobrimos isso por acidente, mas podemos usar isso para influenciar diretamente o tamanho dos poros do objeto impresso”, diz Masania.
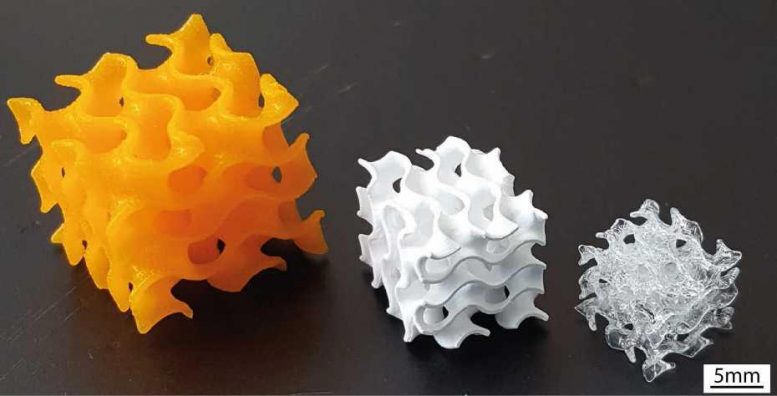
A peça bruta (esquerda) é disparada a 600 graus para eliminar a estrutura plástica. Numa segunda etapa de queima, o objeto se transforma em vidro (direita). Crédito: Grupo de Materiais Complexos / ETH Zurique
Os pesquisadores também conseguem modificar a microestrutura, camada por camada, misturando sílica com borato ou fosfato e adicionando à resina. Objetos complexos podem ser feitos de diferentes tipos de vidro, ou até mesmo combinados em um mesmo objeto utilizando a técnica.
Os pesquisadores então queimam a peça produzida dessa forma em duas temperaturas diferentes: a 600˚C (1.100˚F) para queimar a estrutura do polímero e depois a cerca de 1000˚C (1.800˚F) para densificar a estrutura cerâmica em vidro. Durante o processo de queima, os objetos encolhem significativamente, mas tornam-se transparentes e duros como o vidro de uma janela.
Pedido de patente submetido
Esses objetos de vidro impressos em 3D ainda não são maiores que um molde. Grandes objetos de vidro, como garrafas, copos ou vidraças, não podem ser produzidos desta forma – o que não era o objetivo do projeto, enfatiza Masania.
O objetivo era provar a viabilidade de produzir objetos de vidro de geometria complexa usando um processo de impressão 3D. No entanto, a nova tecnologia não é apenas um artifício. Os pesquisadores solicitaram uma patente e atualmente estão negociando com um grande revendedor suíço de artigos de vidro que deseja usar a tecnologia em sua empresa.
Referência: “Impressão tridimensional de vidros multicomponentes usando resinas de separação de fases” por David G. Moore, Lorenzo Barbera, Kunal Masania e André R. Studart, 11 de novembro de 2019, Nature Materials.
DOI: 10.1038/s41563-019-0525-y